The Molds
Our molds are carefully crafted to ensure the best designs for your city scapes.
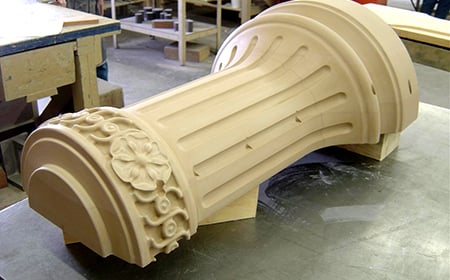
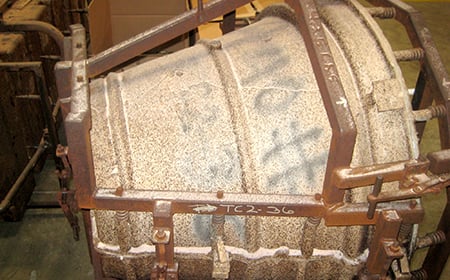
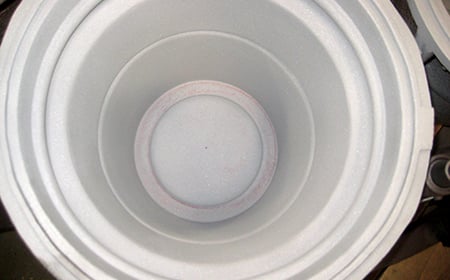
The molds we use in rotational molding are made by fabricating different metals or rolling, bending, and welding sheet metal that range from $6,000.00 to $50,000.00 depending on the size, design, and complexity of the detail work. Aluminum alloys are framed in a cast iron or stainless steel frame, which is fitted with clips to fit into different types of molding machines. The cage style framework allows the machine arms to latch onto it for manipulation near the ovens. It also protects the actual mold, so if the mold falls or hits something, the frame cage takes the impact and the mold retains its shape.
The actual molds are made of a soft aluminum. We take great caution and care to prevent damage to the mold. Preventing water from getting into the mold is crucial. If this happens, the water electrifies in the aluminum, causing tiny holes called porosity that can lead to imperfections in the castings and even explosions in the ovens. If a mold isn’t sealed completely, powdered resin can escape and the piece will not come out right. Any scratches or scrapes inside the mold will all transfer onto the castings, so each piece will have a scar in the shape of the scrape in the mold. Any mold left outside in the elements is subject to rusting and corrosion.
The molds weigh anywhere from 60 to 800 pounds and, unlike the durable resin products they create, are susceptible to degradation problems if improperly cared for. TerraCast® has many product lines, each made from many molds. The molds cannot be stacked or nested. We store them on racks in warehouses or a “mold yard” with the clamshell fastenings closed to keep moisture out. TerraCast® has around 280,000 square feet of warehouse space for our molds since one mold can be used for years as long as it is stored and maintained properly.
We also have an annual maintenance schedule. Every year, the molds are taken out of production for inspection. Our maintenance team inspects for any imperfections. They drill out any porosity and fill the repair site with molten aluminum, sand out any seams and prep the mold for re-entry into production. Most molds can be used for 7,000-8,000 castings before they need serious maintenance. Some of the original RotoCast molds made in the 1970s by our founder, Bob Grossman, are still in production today from the meticulous care we take in maintaining our molds.
Mold makers were traditionally metal workers. They worked in foundries casting molds into a black sand powder and a casting was made from an aluminum part. They poured molten aluminum into the sand casting and allowed it to harden. Then broke away the sand and the hardened aluminum would be the mold. Extremely large molds were made in pieces and then welded together before fitting them for the outer framework cage. Now we have CAD drawings and CNC routers, which cut out a very exact female plug-in part to create the mold, removing the element of human error. In a generalized sense, things have changed recently with the advent of CAD drawing and 3-D printing. The way we make the molds is evolving, along with our methods for coloring and blending.
About Us
All of our products are made in America. All offices, warehouses, facilities and factories stand proud on US soil. Originally founded in 1969, we have remained an American owned and operated company.
Our Products
A Terracast® product is designed to beat out the competition in every conceivable way. Our products are customizable, lightweight, weather/graffiti resistant, eco-friendly, and almost indestructible.
Contact Us
When you contact Terracast® you will always be met with a friendly voice. We want to make sure you are well taken care of whether you're a new customer or have been doing business with us for 20 years.